Examples and Work Flow in the Production module - Sub-Assemblies with Production Operations (Phantom Items)
Examples and Work Flow in the Production module:
---
It is likely that a complex Production process with several assembly stages will use sub-assemblies. You can configure Production Operations to take sub-assemblies into account.
The first stage in building the example hifi rack is to construct the metal shelf frames by welding square-section metal tubes together. These metal shelf frames could be considered to be sub-assemblies, since the same shelf frame could be used in different Production processes (for example, hifi racks with three, four and, as in the example, five shelves).
Follow these steps:
- Create a new Item for the metal shelf frame. This should be a Plain Item. Select the Not For Sales option if you do not want it to be possible to sell the Item (it will not be included in the Items 'Paste Special' list when you open it from a sales record such as a Quotation, Sales Order or Sales Invoice).
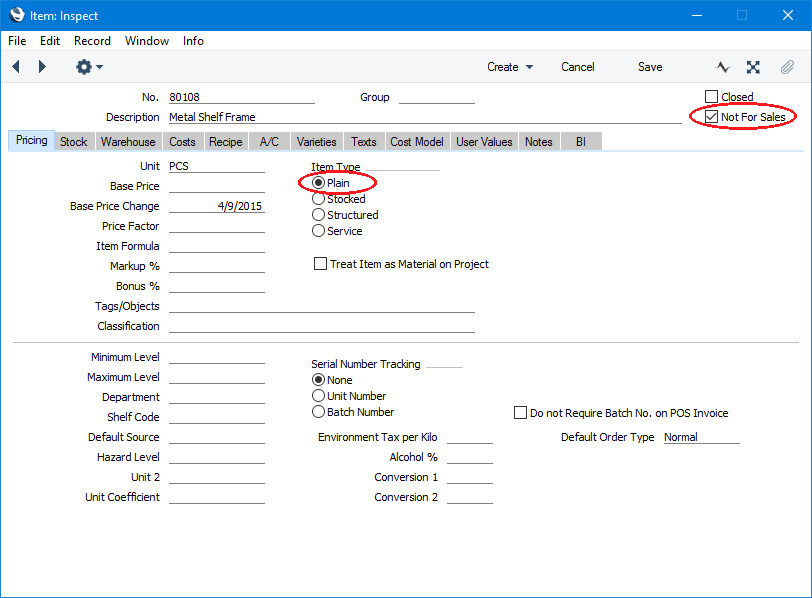
- Create a Recipe for the Item. In this example, the metal shelf frame will be made up using the 40 and 50 cm lengths of steel box section that were in the original top-level Recipe. Although the top-level Recipe requires five frames, the result of the sub-assembly Recipe should be one unit (in the Normal Prod Qty field). This gives you the flexibility of being able to use the sub-assembly in other Production processes with the appropriate quantities:
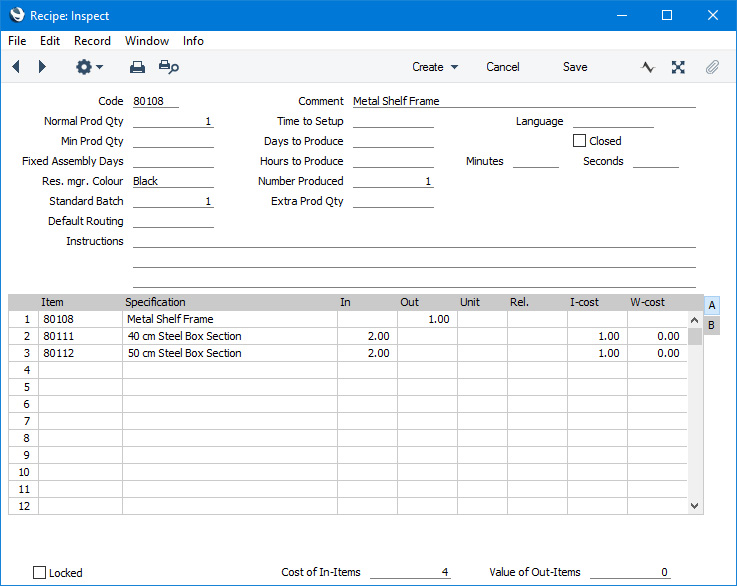 On flip B, enter the same Material that was used for these components in the top-level Recipe:
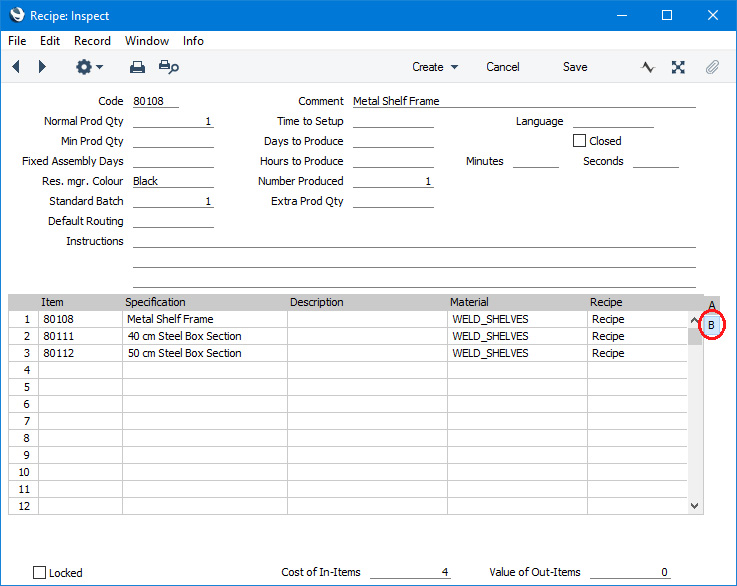 If one of the components is itself a Plain Item with a Recipe, do not specify a Material here but in the Recipe that produces that Item.
- Return to the Item from step 1 and enter the Recipe in the Recipe field. This Item is now a "Phantom" Item. A Phantom Item is a Plain Item with a Recipe. It is an Item that only exists momentarily during the Production process. Because of this, it is not an Item that can be sold, and therefore you may want to mark it as Not For Sales as shown in the Illustration in step 1. This will mean the Item will not be included in the Items 'Paste Special' list or in the Price List report.
- Open the top-level Recipe and replace the components representing the two lengths of steel box section with the new Phantom Item, with the appropriate In Qty:
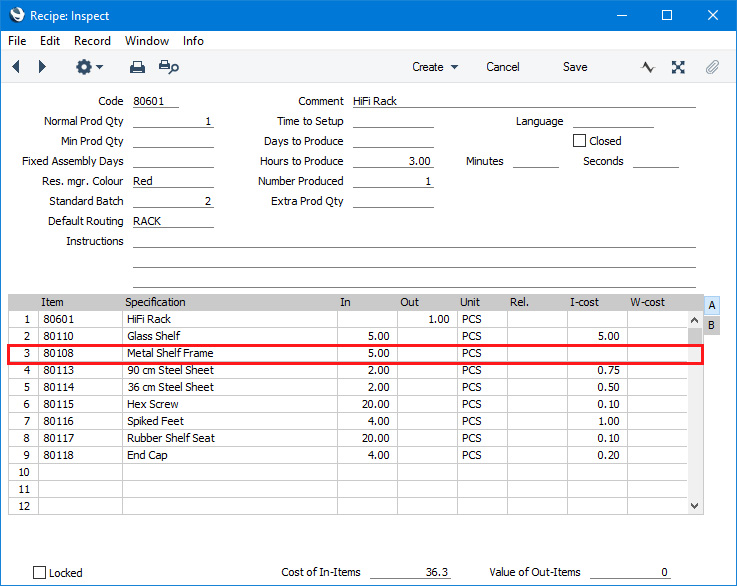 On flip B, make sure that the Phantom Item does not have a Material:
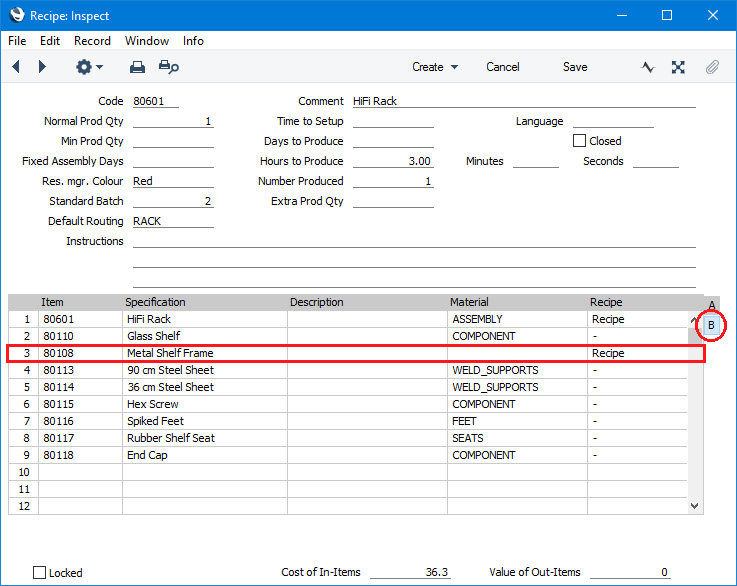 You only need specify Materials for Phantom Items in the sub-assembly Recipe that produces the Phantom Item (as shown in step 2), not in the top-level Recipe. The Material connects the component with the Operation that will remove it from stock. A component that is a Phantom Item is also a Plain Item. So, it is not held in stock and so cannot be removed from stock. If you specify a Material for a Phantom Item in the top-level Recipe, this will be interpreted as an attempt to remove that Item from stock. As a result, you will not be able to complete the Production process and instead you will be told, "Quantity has not been produced yet".
- In this example, we are still using the "WELD_SHELVES" Material: the only change was to move this Material from the top-level Recipe to the Recipe that produces the Phantom Item. There is therefore no need to change the Routing or any of the Standard Operations. If we had used a different Material in the Phantom Recipe, then we would now have to update the Routing and/or the Standard Operations so that the shelf frames would be built at the correct stage in the process.
Remember that each Standard Operation contains a list of the Materials that will be used during a particular stage in the Production process. The Material connects the Standard Operation to some of the Input Items in the Recipe. For example, if the Material is "WELD_SHELVES", all Input Items marked "WELD_SHELVES" will be removed from stock when the Standard Operation is completed. The "WELD_SHELVES" Items can be in the top-level Recipe or, as in this case, in a lower-level Phantom Recipe.
- The configuration work is complete, so you can now use the revised Recipe in a Production. After creating the Production and specifying the Recipe, and after moving stock of the Input Items into the Production Location using Stock Movements, you can use the 'Production Operations' function to create Production Operations.
In our example, the change to the Phantom Item will only affect the first Production Operation. Previously (as illustrated on the Assembly in Stages page), the effect of the first Production Operation was to remove the steel box section from stock. Now, the steel box section will again be removed from stock, but the shelf frames will be produced:
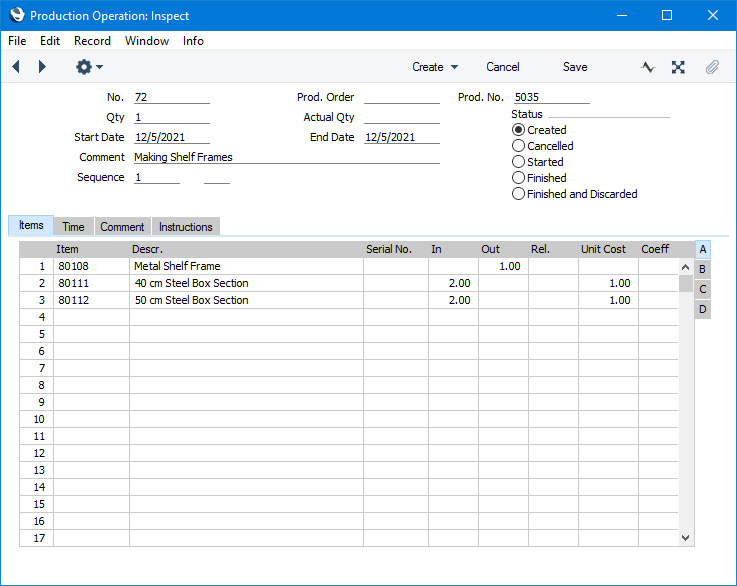 As the shelf frames are Plain Items (and as they will exist for only a short while), they will not be added to stock (they will not be included in the Stock List report) when you Finish the Production Operation. As with other Production Operations, when you Finish the Production Operation, the value of the components will be added to the Work In Progress Account, not to the Stock Account.
- In some cases, it might not be appropriate to use Phantom Items. It might be that the Production process is a long one, in which case you might want components that are produced early in the process to appear in your stock valuation for period they exist (i.e. you want stock levels to be maintained, and you want their value to be held in the Stock Account not the Work In Progress Account). Or it might be that you sell components (spare parts) as well as assembled Items.
If so, change the procedure described above in the following ways:
- In step 1, the Item should be a Stocked Item. You can still mark it as Not For Sales if you want to prevent it being sold as an Item in its own right.
- Create the Recipe as described in step 2 and be sure to specify Materials on flip B.
- Enter the sub-assembly Item into the top-level Recipe as described in step 4. However, as the sub-assembly is a Stocked Item, you should specify a Material on flip B. Usually this will not be the same Material that you used in the sub-assembly Recipe. The Materials in the sub-assembly Recipe will connect the sub-assembly components to a particular Standard Operation i.e. they indicate the stage in the Production process when the sub-assembly components will be removed from stock and when the sub-assembly will be built and added to stock. The Material in the top-level Recipe will connect the sub-assembly itself to a particular Standard Operation i.e. it indicates the stage in the Production process when the sub-assembly will be removed from stock and built in to the final assembly. In the case of the Phantom Item, as it was never added to stock, there is no need to use a Material in the top-level Recipe to specify when it should be removed from stock. Indeed and as previously mentioned, if you do, you will not be able to complete the Production process.
- As already mentioned, the Production Operation that produces the sub-assembly will debit the Stock Account not the Work in Progress Account, as the sub-assembly is a Stocked Item. However, the Production Operation that removes the sub-assembly from stock will debit the Work In Progress Account as normal.
- The Recipe that produces a sub-assembly might itself be a complex multi-stage process and therefore will need its own Routing. If this is the case, the result of the Recipe must be a Phantom Item. In this case, when you create Production Operations from a Production, the relevant Operations both for the final Item and for the sub-assembly will be created. If the sub-assembly is a Stocked Item, then only the Operations for the final Item will be created, not those for the sub-assembly.
If a sub-assembly has its own Routing (and, especially, if the sub-assembly contains a further sub-assembly with a Routing), then you will need to plan the Sequence of the Operations carefully.
The second stage in building the example hifi rack is to construct the two metal supports by pressing metal sheet into shape and welding sections together. We will now convert this stage into a sub-assembly with its own Routing. Follow these steps:
- Create a new Item for the metal support, as described in step 1 above. This must be a Plain Item.
- Create a Recipe for the Item, as described in step 2 above. On flip B, enter the Materials as appropriate:
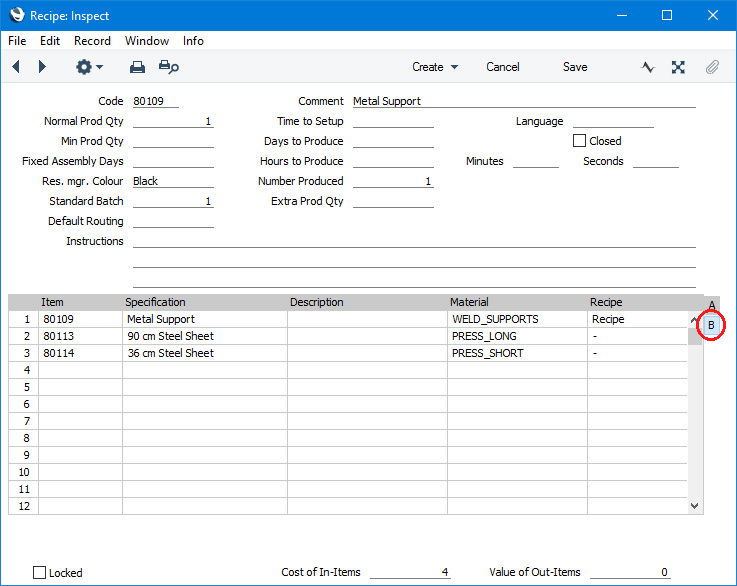
- Return to the Item from step i and enter the Recipe in the Recipe field. Mark it as Not For Sales if necessary.
- As described in step 4 above, open the top-level Recipe and replace the components representing the two sizes of metal sheet with the new Phantom Item:
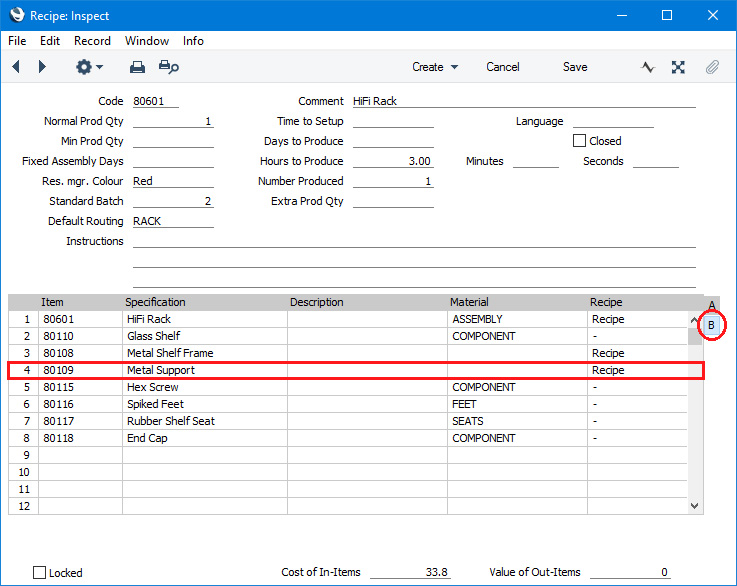 Remove the Material from this Item on flip B.
- Create the Standard Operations and the Routing for the sub-assembly. This is the Routing:
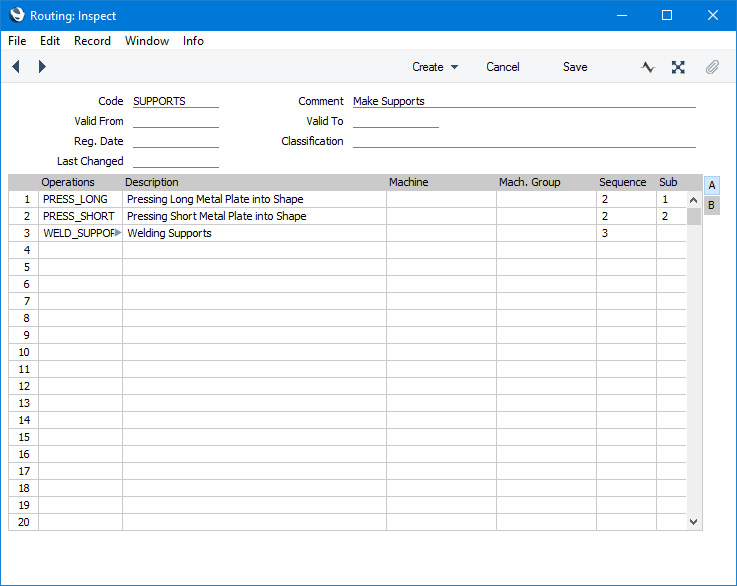 In this illustration, we have used the same names for the Operations as for the Materials for clarity.
The first two Operations have the same Sequence number, but different Sub Sequence numbers. These two Operations represent pressing different sizes of metal sheet into shape, so they can take place simultaneously. The two pieces of shaped metal sheet will then be welded together, so this Operation has a later Sequence number. The Sequence numbers are 2 and 3, to fit in with the top-level Routing.
- Return to the Recipe from step ii and enter the Routing in the Default Routing field:
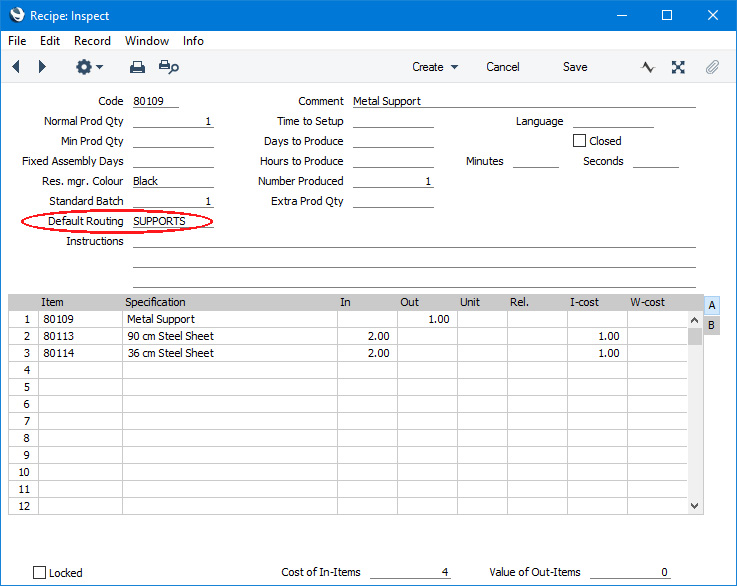 - Open the top-level Routing and adjust the Sequence numbers so that the sub-assembly will fit in correctly:
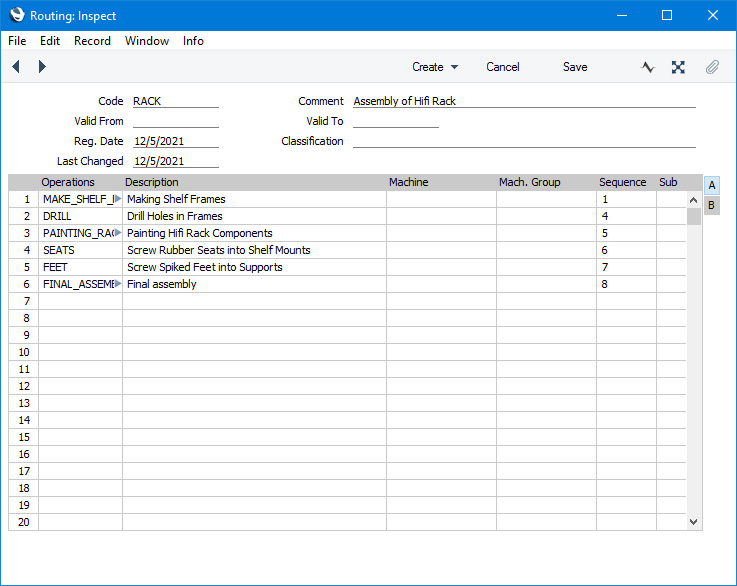 Note the gap in the Sequence for the sub-assembly.
Note too that there is no reference to the sub-assembly in the top-level Routing. The function that creates Production Operations from a Production will first check the Production for Phantom Items with Routings (i.e. for Plain Items with Recipes that have Routings) and create the relevant Production Operations (for the sub-assemblies). It will then refer to the top-level Routing (the one quoted in the Production) and again create the relevant Production Operations (for the top-level Item). So the Production Operations will not be created in the correct sequence, but the Sequence numbers will ensure you can execute them in sequence:
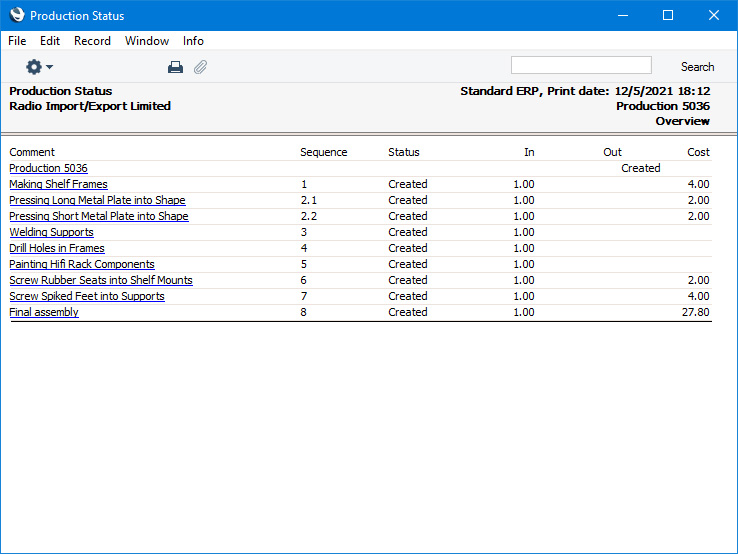 It would of course be possible to fine-tune the sequence so that the supports and the shelf frames are built at the same time. An added refinement might be to add a Routing to the Recipe that builds the shelf frames to move the drilling of holes (currently step 4 in the sequence) from the top level to the sub-assembly level.
---
Examples and Work Flow in the Production module:
See also:
Go back to:
|