The Production Item Alternative register in Standard ERP
The Production Item Alternative register connects Output Items, Machines and Recipes. You should enter a separate record in this register for each Output Item that you produce. Use this record to list the Machines that you can use to produce the Output Item, and the Recipes that you will use with each Machine.
The information in the Production Item Alternative register will be used in the following situations:
- When you specify a Recipe in a Production Order and if you have entered a record in the Production Item Alternative register for the Output Item in that Recipe, the Default Machine from that record will be copied to the Production Order. If that Production Item Alternative record does not have a Default Machine, the Machine in the first row with the Recipe will be used.
- If you create a Production Order using the 'Create Planned Records from Ordered Items' or 'Create Planned Records from Orders' Maintenance functions in the Sales Orders module or the 'Create Productions' Maintenance function in the MRP module, the Machine in that Production Order will be chosen as described in the previous point.
- If you change the Machine in a Production Order, you must do so to a Machine that is listed in the Production Item Alternative record for the Output Item (i.e. to a Machine that can produce the Item). You can change the Machine in a Production Order itself or by dragging and dropping the Production Order from one Machine to another in the Resource Planner. If the new Machine uses a different Recipe, that Recipe will be copied to the Production Order, and the Input and Output Items will be changed accordingly.
To work with Production Item Alternatives, first ensure you are in the Production module. Then, if you are using Windows or macOS, click the [Registers] button in the Navigation Centre and double-click 'Production Item Alternatives' in the resulting list. If you are using iOS or Android, tap the [Registers] button in the Navigation Centre and then tap 'Prod. Item Alternatives' in the 'Registers' list. The 'Production Item Alternatives: Browse' window will be opened, showing the Production Item Alternative records that you have already entered. To enter a new record, select 'New' from the Create menu (Windows/macOS) or the + menu (iOS/Android). or use the Ctrl-N (Windows) or ⌘-N (macOS) keyboard shortcut.
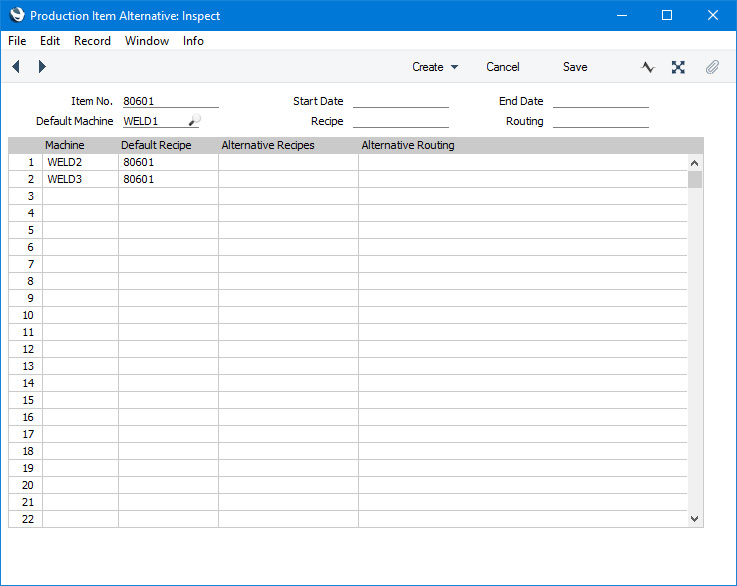
- Item No.
- Paste Special
Item register
- You should enter one record to the Production Item Alternative register for each Output Item. Specify the Output Item here. The Production Item Alternative record should be a list of the Machines that you can use to produce the Output Item, and the Recipes that you will use together with those Machines.
- Start Date, End Date
- Paste Special
Choose date
- If the Production Item Alternative record can only be used for a certain period, specify that period using these fields.
- This period is only used by Production Plans. If you have entered Start and End Dates in a Production Item Alternative record and you enter the Item specified above in a Production Plan that falls between those dates, the Recipe in that Production Item Alternative record will be copied to flip C of the Production Plan row. Otherwise (i.e. if the relevant Production Item Alternative record does not have Start and End Dates), the Recipe on flip C of a Production Plan row will be taken from the relevant Item record.
- Default Machine, Machine
- Paste Special
Asset module, Assets module
- The Default Machine should be the Machine that you will usually use to produce the Item in the field above. Use the grid to list the other Machines that can produce the Item together with the Recipes that those Machines will use.
- The Default Machine will be copied to all Production Orders where the Item is the Output Item.
- If you do not specify a Default Machine, the Machine copied to Production Orders that you enter yourself will be the Machine in the row containing the Recipe that you enter in the Production Order. Production Orders that you create using the various Maintenance functions will use the Machine in the row containing the Recipe specified in the Item record. Therefore, if you do not specify a Default Machine, be sure to enter a row with the Recipe used in the Item record and appropriate Machine.
- If you change the Machine in an existing Production Order, the Recipe in that Production Order will be changed as well, to the Recipe in the row with that Machine. The Input and Output Items will be changed accordingly.
- When you save a Production Order, a check will be made that the Machine can produce the Item (i.e. the Machine is listed in the Production Item Alternative record for the Item).
- Recipe, Default Recipe
- Paste Special
Recipe register, Production module
- Having entered a Default Machine in the header and listed alternative Machines in the rows, you should also specify the Recipes that those various Machines will use. You can use the same Recipe with several Machines.
- The Recipe in the header will be used as a default in only one circumstance. If you have entered Start and End Dates in a Production Item Alternative record and you enter the Item in a Production Plan that falls between those dates, this Recipe will be copied to flip C of the Production Plan row. Otherwise (i.e. if the relevant Production Item Alternative record does not have Start and End Dates), the Recipe on flip C of a Production Plan row will be taken from the relevant Item record.
- If you change the Machine in an existing Production Order, the Recipe in that Production Order will be changed as well, to the Recipe in the row with that Machine. The Input and Output Items will be changed accordingly.
---
See also:
Go back to: