Create Planned Records
This function will be useful in businesses that operate on the 'Just In Time' principle whereby
Purchase Orders for Items on Sales Orders are raised as late as possible, so that the goods arrive just before they are scheduled for delivery to the Customer. It creates Purchase Orders and Productions for Items on Sales Orders dated according to the
Planned Delivery Dates of the Sales Orders and the
lead times of the Items in question. These are sometimes known as "Future" or "Planned" records. The Planned Delivery Date field must use the Date format, set in the
Planned Delivery setting, if you wish to use this feature.
The function will find all unfulfilled Sales Orders whose Planned Delivery Dates fall within the specified period. Usually, a separate unapproved Purchase Order will then be created for each Date/Supplier combination. These can be printed out and approved at the appropriate time from the 'Purchase Orders: Browse' window, sorted by Trans. Date. The exceptions to this are noted in the field descriptions underneath the illustration. If any of the Items on the Sales Orders are Stocked Items with a Recipe specified on the 'R
ecipe' card, records will be created in the Production register facilitating the assembly of these Items, and Purchase Orders will be raised for the components.
Suppliers will be selected for Items as follows:
- If an Item has a corresponding record in the Purchase Item register in the Purchase Orders module with a Supplier specified and with the Default check box switched on, that Supplier will be used. Please refer here for details of Purchase Items.
- In all other cases, the Supplier will be the Default Supplier specified in the Purchase Order Settings setting. If no Default Supplier has been specified, Purchase Orders will not be raised for Items that do not meet the criteria in point 1 above.
The
dates of the Purchase Orders will be calculated from the
Planned Delivery Dates of the Sales Orders and the
Delivery Days of the Purchase Items. For example:
Planned Delivery Date of Sales Order | 25/1/2003 |
Delivery Days of Item 1 (from Purchase Item) | 10 |
Delivery Days of Item 2 (from Purchase Item) | 5 |
| |
Date of Purchase Order for Item 1 | 15/1/2003 |
Date of Purchase Order for Item 2 | 20/1/2003 |
If an Item is being purchased from the Default Supplier (point 2 above), the Delivery Days is assumed to be zero.
For Stocked Items with Recipes, it will be necessary for Production records to be created. Their dates will take into account the Fixed Assembly Days and the Days to Assemble each Unit recorded in the Recipes. If Purchase Orders are created for the components, these will be dated so that the components arrive in time to carry out the assembly.
Selecting the 'Create Planned Records' function brings up the following dialogue box:
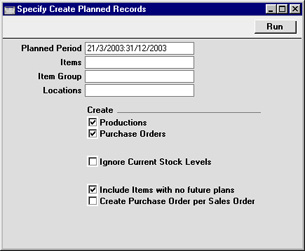
- Planned Period
- Paste Special
Reporting Periods setting, System module
- Purchase Orders and Productions will be created from all Sales Orders whose Planned Delivery Dates fall in the period entered here. If a particular Order row has a Planned Delivery Date on flip E, this will be used in place of that on the 'Date' card: in fact the 'Date' card field can be blank if all rows have their own date. The Planned Delivery Date must use the Date format, set in the Planned Delivery setting.
- The default period runs from the current date to the last day of the first period in the Reporting Periods setting.
- Any Closed Orders with Planned Delivery Dates falling in the selected period will be ignored.
- Items
- Paste Special
Item register
- Range Reporting Alpha
- To create Purchase Orders and Productions for specific Items, enter an Item Number or range of Item Numbers here. Only Items in the range that have been used in the selected Sales Orders will be ordered.
- Only Stocked Items are ordered: Plain, Structured and Service Items are ignored.
- Item Group
- Paste Special
Item Group register, Sales Ledger
- To create Purchase Orders and Productions for Items belonging to a specific Item Group, enter an Item Group here. Only Stocked Items in the Group that have been used in the selected Sales Orders will be ordered.
- Locations
- Paste Special
Locations setting, Stock module
- If this field is blank, the function will create one Purchase Order for each Supplier/Date combination, subject to the Create Purchase Order per Sales Order option below. So, Items on various Sales Orders which can be purchased from the same Supplier and which have to be ordered on a particular date will be placed on a single Purchase Order. The Location field on the 'Del Address' card of this Purchase Order will be blank. Sales Orders with and without Locations (specified on the 'Del Terms' card) will be considered.
- If this field contains a Location, the function will create separate Purchase Orders for each Supplier/Date/Location combination. The appropriate Location will be shown on the 'Del Address' card of the Purchase Order. Only Sales Orders with the appropriate Location (specified on the 'Del Terms' card) will be considered. No attention will be paid to any Location entered on flip F of the Sales Order.
- Usually, only one set of Purchase Orders and Productions will be created from a particular Sales Order. Repeated use of the 'Create Planned Records' function will not result in many Purchase Orders. However, in the case of Sales Orders with Locations, if you first run the function for specific Items (or with a blank specification window) and then for a specific Location, you will get two Purchase Orders, one with a Location on the 'Del Address' card and one without. It is therefore recommended that you make sure that you always specify a Location or always leave the Location field blank, as appropriate.
- Create
- Use these options to determine whether Purchase Orders and/or Productions are to be created.
- If you choose to have Productions created only, Purchase Orders will still be created for the components.
- Note: when entering Recipes, the last row should always contain the Item Number of the output Item (i.e. the Item being produced). If a Recipe is entered where this is not the case, this will cause problems when this function attempts to create a Production using this Recipe.
- Ignore Current Stock Levels
- By default, the quantity on any Purchase Orders and Productions will take current stock levels into account. For example, you have a Sales Order for five of a particular Item of which you already have three in stock. The function will create a Purchase Order with a quantity of two. The Minimum Order Quantity from the Purchase Item will be taken into account.
- If this box is checked, the quantity will be copied from the Sales Order to the Purchase Order, and current stock levels will be ignored. So, in the example, a Purchase Order with a quantity of five will be created. Again, the Minimum Order Quantity from the Purchase Item will be taken into account.
- Create Purchase Order per Sales Order
- The function will usually create one Purchase Order for each Supplier/Date combination or each Supplier/Date/Location combination, depending on whether you specified a Location above. Items on various Sales Orders that can be purchased from the same Supplier and that have to be ordered on the same date will be gathered together on a single Purchase Order. If an unapproved open Purchase Order with the appropriate Supplier, Location and Date already exists, a new Purchase Order will not be created and instead Items will be added to the existing Purchase Order.
- If instead you would like separate Purchase Orders to be created for each Sales Order, check this box. This only affects the function if you have specified a Location in the field above.
Click [Run] to run the function. It may take a few moments, depending on the number of Purchase Orders and Productions to be created. When it has finished, you will be returned to the 'Maintenance' list window.